A flywheel is a heavy wheel that stores kinetic energy…
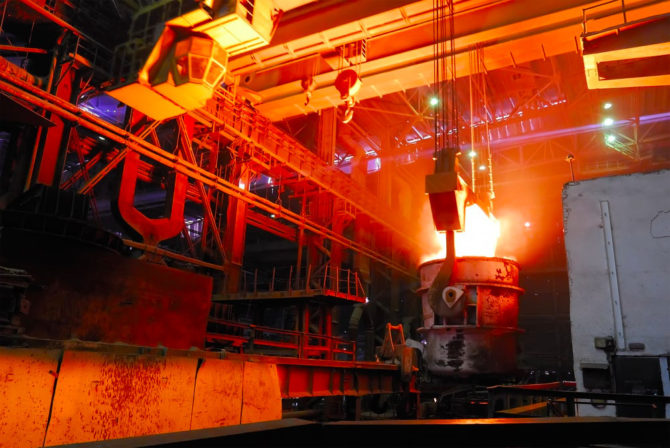
Top Industrial Casting Product Manufacturers Driving the Industrial Growth
The market for industrial castings in India is growing fast, mirroring the trends in the global markets. Over the 2021-2025 period, the CAGR of this sector is expected to be around the 10.2% mark – with high-quality casting products increasingly finding usage in many industries, right from heavy equipment, machine tools and automobiles, to electrical motors, industrial plants, and even household appliances. Leading industrial casting manufacturers are playing a critical role in transforming the industry and bolstering growth.
Over here, we will take a look at how these manufacturing firms are driving industrial growth:
Ensuring Best-In-Class Product & Process Diversity
The best manufacturers invariably have a vast range of casting product designs, sizes and applications on offer. Buyers can benefit from the powerful and varied capabilities of these dynamic casting tools and accessories – and the products are, in most cases, seamlessly integrable with other existing machinery. The top industrial casting products deliver an ideal combination of service excellence, quality and budget-friendliness. The manufacturing companies have professional certifications (ISO 9001:2015, OHSAS 18001: 2015 and others) – and they are adept at delivering high-utility casting solutions for industrial and agricultural sectors, automotive plants, counterweights and other requirements.
Supplying Designs For Different Applications
By using premium-grade casting materials (metals and alloys) and following economical, efficient workflows, foundries are able to prepare casting products of intricate and increasingly innovative shapes – for stronger, better mechanical performances. Flowing designs are incorporated, for greater convenience. In this context, the growing role of 3D modeling technology in present-day casting product manufacturing at leading foundries also needs to be highlighted. These companies typically look to establish uniformly smooth collaborations with their clients – and the latter can also preview the casting product(s) before production. This ensures higher mechanical precision and accuracy, and minimises the uncertainty factor.
Quality Assurance; Zero Glitches
In the face of rising competition, industrial casting manufacturers in India, USA, UAE, Africa are increasingly focusing on delivering casting tools of the optimal quality. The in-house experts have the necessary skill and technical acumen to design casting products that are dimensionally accurate and have top-notch consistency. Due care is taken to ensure that the die blocks are not deformed during the manufacturing process – while the companies also minimise scrap loss, thereby pulling down the overall cost of production as well. Quality monitoring and checks are performed throughout the production process, to ensure flawless, precision designs, and high-quality surface finishes. Smart automation has also proved to be immensely valuable in designing highly durable casting products that deliver the desired performance.
Following The Best Practices For Casting Product Manufacturing
Manufacturers and suppliers of top industrial casting products follow the latest, cutting-edge industry practices, to deliver buyer satisfaction. Machining requirements are minimal after production, and high-quality lubricants are used to manage the die temperature levels. Design uniformity is maintained at all stages – and the high shape and size tolerances add to the durability factor of the casting products. In general, metal castings deliver higher cost-effectiveness in bigger product runs (production volumes). Many casting product manufacturing companies also supply industry-grade sand casting and investment casting solutions as well. There are no maintenance hassles either.
Utilisation Of State-Of-The-Art Facilities
Modern-day foundries typically have world-class facilities for delivering end-to-end industrial casting solutions. There are fully equipped physical, painting, and chemical laboratories onsite, and the latest vacuum molding/hand molding techniques are used. Powerful fabrication units are set up, for creating high-class casting products and customised pellets. Leading casting product manufacturers, like Crescent Foundry, always focus on constant improvement and adherence to high-integrity core business values. By adopting viable material recycling policies and minimising wastage, production procedures are kept eco-friendly. Most good casting manufacturers engage in important CSR (corporate social responsibility) activities as well.
Industrial Casting Manufacturers Provide Greater Freedom and Efficiency
With the advancement of mechanical efficiency and technology, foundry casting has become more efficient than ever before. Manufacturers strive to maximise operational efficiency levels, reduce labor expenses, and optimise the assembly lines & speed of production. The strength and usability of top-grade industrial casting is significantly more than that of metal fabricating. Casting tool manufacturers make it a point to understand the precise nature of client requirements, and solutions are delivered accordingly. Full transparency is maintained in all buyer-supplier interactions – and the best casting product suppliers also have the know-how to identify and eliminate all possible problems prior to the production process.
Ensuring Enhanced Longevity & Performance Assurance
To ensure optimal value, renowned casting product manufacturers ensure that their tools have the requisite mechanical properties. In general too, it is relatively easy to cast different materials (both ferrous and non-ferrous), while various casting sizes can be supported as well. Uniformity of the casting products is ensured by the low cooling rates at the manufacturing facilities. The tools designed by reliable foundries also have excellent shock-resistance and electrical properties – while they are rust-resistant too, and are likely to have minimal mechanical fatigue (i.e., wear and tear). As such, these casting products offer superior performance over a long period of time.
Providing Top-Class Reliability & Durability
Industrial casting activities are evolving constantly. Casting designs and manufacturing standards are becoming smarter – and most casting manufacturers follow and implement these latest production methods. The mechanical properties of the casting products are tested regularly, to ensure full reliability and elimination of leakage risks in future. Agile and streamlined manufacturing processes are followed, to shorten production lead-times and facilitate quick transitions from raw materials to final casting tools. The efficient workflows bring down fabrication costs considerably as well. With technological innovation, casting has become way more efficient and flexible than stamping, forging and welding.
Improved Adaptability and Economy
While manufacturing top industrial casting products, extra metal/materials are recycled and reused by leading foundries. These companies constantly endeavor to increase the adaptability of their manufacturing workflows as well as the final products, in line with the mass production requirements. Since there is practically no wastage, there are more economies of scale, and ROI levels are higher. From less than a kilogram to hundreds of tons, casting tools can be of different weights – as per the needs of the different projects. Robust safety policies are also adopted during the production stages, as well as for the final users. As the variety of casting products is expanding, the scope of their applications is going up.
Added Reading: Top Industrial Casting Product Manufacturers Driving the Industrial Growth
Lower Costs & Better Returns
Most well-known manufacturers and suppliers of industrial castings use competitively-priced and readily available raw materials while maintaining best-in-class production standards and facilities. Hence, the capital investment required by these firms is on the lower side. Production costs are kept at manageable levels as well. There are no limits on weight, size, and/or production volume either – and by eliminating chances of shrinkage, cracks, and shape defects, stability levels are maximized. Certain metals can only be cast due to their respective metallurgical features. The overall manufacturing costs are reasonable, and buyers can get the best industrial casting products without having to go beyond their budgets.
Foundry 4.0 – with its latest technological innovations, systematic procedures, efficient workflows, and increasingly wider applications – is well and truly upon us. The number of end-users/customers is increasing exponentially, along with the number of reliable foundries and specialized industrial casting manufacturers. The ecosystem of casting products is set to become more robust than ever before – boosting sustainability, profitability, and usability.