In sync with global trends, the Indian market for ductile…
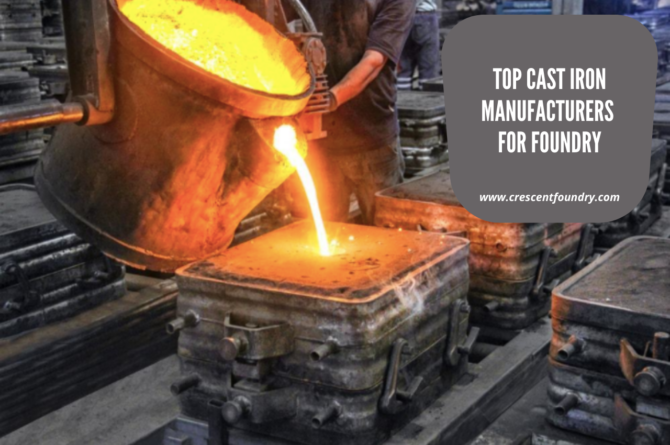
Top Cast Iron Manufacturers for Foundry
Cast iron products have been part of human lives for centuries. From any historical artwork to kitchen skillet cast iron, manufacturers have cast their importance in day-to-day life. Metal castings are commonly made up of gray iron is a ferrous alloy metal extracted from iron ore. Cast iron naturally has a carbon content of around 2% to 4%. Its crystalline structure gives it excellent strength in compression, though it is weaker in tension and high carbon content makes it relatively brittle. The brittle nature of the cast iron makes it easily prone to repairs and damages. Damages can occur in many ways due to chemical corrosion and galvanic corrosion. Cast iron products may be challenging to repair, but cast-iron manufacturers ease this process as they help their customers repair the cast iron cracks themselves. The cast iron cracks repairs are done in the foundry where the castings are produced. Frequently, cracked cast iron parts are repaired by welding and metal stitching methods. The cast iron cracks are not unusual; cast iron’s brittle nature makes it easily prone to damage as the iron ages.
Cast iron cracks
When metal castings are made, molten iron is poured into a mould and allowed to cool slowly. This high carbon content material is allowed to cool slowly to create crack-free castings. Therefore while repairing cracks, when welding cast iron before or after welding, the cast irons must be allowed to slowly cool or should be kept cool enough to get better outcomes. Before starting the repairing process, Foundries take the first most step to identify the products’ cast iron type, characteristics, and structure. Every kind of ferrous metal requires a unique repair methodology. The cast iron manufactures metal castings from processed iron ore which is naturally relatively stable. The processed cast iron products seek to return to their original state through corrosion. Two types of deterioration occur to cast iron; they are chemical and galvanic corrosion.
When cast iron products are exposed to air and water for a prolonged period of time, the metal loses its electrons to a non-metal substance such as oxygen. This iron oxidation process causes chemical corrosion. Galvanic corrosion is also known as bimetallic corrosion. It occurs when two dissimilar metals are placed in direct contact with one another in water. The potential of corrosion should always be considered when repairing cast iron cracks. Acquainting with different metals can have severe consequences on the longevity and effectiveness of maintenances. Cast Iron products or parts are usually painted or coated to prevent moisture and minimize air contact with the metal surface.
Role of cast iron manufactures in repairing cast iron cracks.
When commissioning repairs, it is essential to understand the significance, types, characteristics and aesthetics of the cast iron parts; so that any interventions can be planned systematically. Finding the right personnel or company is one of the most key aspects of any repair job. The aiding cast iron manufacturers should have previous experience and sound knowledge of basic conservation principles working with cast iron products. They should be equipped with adequate technology instruments and appropriately skilled professionals to carry out repairs sensitively. Each industry type functions with a different set of cast iron products varied on size, shape and material combination. Every unique product requires distinct repair methodology procedures to repair the damages.
Foundries assist many industries not only to cast their products but also to carry out repair work. With years of experience in the field, foundries have executed the process and technique of crack repair in cast iron casting and heavy bronze equipment by welding, metal lock and metal stitching. They prefer using pneumatic light-weight tools and expert technicians to successfully undertake the crack repair in all types of products manufactured out of cast irons. The restoration of broken metal casting by metal stitching and metal locking process is a new methodology of repair that is now acclaimed worldwide, including sectors like defence, agriculture, oil and gas, aviation, automobile, and the industries using critical equipment.
The process involved in repairing a crack in cast iron
The repair of components manufactured out of cast iron by welding is a standard method. Nowadays, due to technology advancements, metal locking or metal stitching cold process has become quite common. Foundries are fixing the cracked or broken metal castings by securing the two disparate metal pieces back together using a metal stitching or metal locking process. This exclusive technology has offered repair services benefiting a variety of industrial purpose. The metal stitching or metal locking process is a precise mechanical method using a cold repair mechanism for making permanent repairs of broken cast iron machine components. All the cracks and fractures, irrespective of cast iron products’ length and width, can be repaired successfully by the metal stitching process. All cracks developed in large and heavy equipment like cylinder heads, cylinder liners, turbocharger casings, pistons and damaged blocks due to excessive stress, accidents or ageing, can be repaired by metal locking.
Welding is one of the oldest methods used in repairing cracks in cast iron. In general, it is preferred to weld cast iron with or without preheating. For the crack repair of cast iron components, planning is done based on its stress, load characteristics and applications. Breakages or cracks usually occur because of overloading, accidents, equipment misuse or flaws in the operating. Depending upon the casting circumstances, the repair is done with or without preheating procedure. Because of cast iron’s crystalline nature, tiny cracks tend to appear next to the weld even when reasonable procedures are followed. Thus sealing the cracks is an essential step followed in the welding process.
Why metal locking preferred over welding?
The cast iron manufacturers in India, USA, UAE, Africa have developed special tools, fixtures, jigs, and materials to perform ingenious repair procedures. These tools enable the successful cold repair of all types of machines and restore cast iron components. The brittle nature of the cast iron products makes it needs to be cold to perform repairs or mending. As a cold process method, metal locking or metal stitching offers an ideal alternative solution to welding in applications where heat is not endorsed. The metal stitching process dampens and absorbs compression stresses providing a good expansion joint for such castings as cylinder liners, cylinder heads or any component subjected to thermal stresses. It distributes the tension load evenly away from fatigue points and maintains alignment since lack of heat produces no distortion. Again, the metal locking method requires little or no dismantling steps, thus saving time and money. These features make metal stitching preferable to welding.