As the global automobile sector is getting more and more…
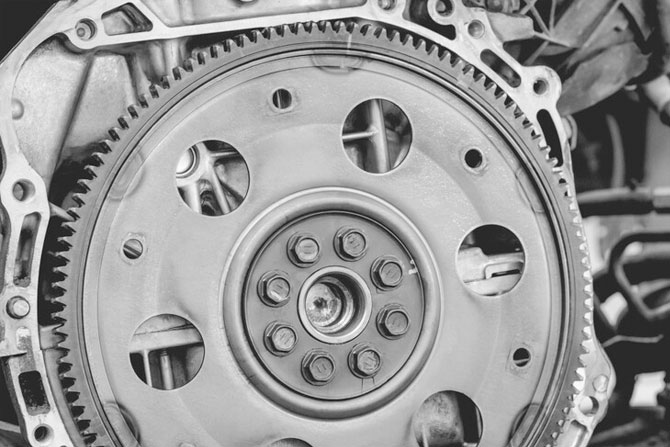
Things to Look While Choosing The Best Flywheel for Your Business
The demand for automotive spare parts has increased immensely due to the astounding growth in the automobile sector. This established growth in automobile industry has geared up enormous automotive parts manufacturers to produce more to meet the global market demands. In any automotive engine, flywheel plays a significant role in the functioning of the machines. A flywheel is a component used to store the kinetic energy when the need for energy is less required than generated and deliver power to the engine when needed. In olden days, Flywheels were created initially for a sole purpose to keep machines running smoothly from one cycle to cycle another, later installed in every automobile engine built. As the world keeps pacing with change and development, flywheels and flanges are used for various industrial purposes. Nowadays, flywheel manufactures produced variety of flywheels in respective sizes and shapes as per each industrial needs. Ductile iron, nodular iron, Chromoly alloy, billet aluminium and billet steel are the materials used in manufacturing flywheels. Flywheels are used widely in automotive, railways, oil and gas industries for smooth operations. India’s top flywheel companies have attained an important place in the global market through adequate quality raw material supply and inexpensive labour.
Flywheel and its functions
The flywheel is a rotating disc in the shape of wheels installed with the machines’ rotating shafts. To maintain efficient rotation of the engines, flywheels rely on a moment of inertia. It is engaged with the engine’s starter motor with its gear teeth and firmly attached to a flange of the crankshaft inside the bell housing. Once the engine starts its transmission, flywheel acts as an energy bank to store kinetic energy and give the motor power when requisite. It is made up of cast iron, steel or aluminium depending on its applications. Flywheel manufactures produce too rigid products to prevent flexing or wearing during swift rotary movement’s usage. Flywheel function is very simple, like aiding engine operation without stalling and balances the engine with its specific weight. During transmission, flywheel enhances the power to the wheels through a clutch. The main advantage is that they sustain the momentum and dampen down speed fluctuations of the engine or electric motor. Flywheels are available in both small and large diameters, heavier or lighter varying the usage of applications. Usually, large flywheels with heavy nature store more kinetic energy and are preferred for heavier vehicles like trains and trucks.
Factors to consider before choosing the best flywheel
Choosing the best flywheel for the intended business application will significantly affect drivability, performance, and safety. Each industry application varies; thus, flywheel manufacturers produced flywheels using iron or composite materials in different sizes and weights to meet the demand on their customers in the global front as per each industry requisite.
Flywheel size and weight
Selecting the proper flywheel weight is a crucial step in enhancing the engine or electric motor’s performance.
Standard weight flywheels
These are heavier flywheels store more kinetic energy and allow engines to work under loads. Moreover, it can slow the throttle response and sustain engine speed longer on deceleration. These flywheels are a noble choice for cars consistently pulling heavy trailers like stocked geared vehicles, trucks, trains, trams etc. Cast iron or nodular iron and billet steel flywheels weigh around 25 to 40 lbs.
Lightweight flywheels
These are lighter in weight and boost the engine to run at high speeds, for better acceleration and deceleration. These are the preferred choice for race cars motorsport and circle track, instantly changing the engine’s dynamics. Billet aluminium flywheels weigh around 10 to 18 lbs, and Chromoly flywheels weigh about 14 to 21 lbs.
Single mass flywheels
These solid mass flywheels are made out of a single piece of heavy metal or steel, and it is connected directly between the clutch assembly unit and the engine. These discs have more outstanding thermal and warp resistance, thereby improving durability and resurfacing. Single mass flywheels allow faster engine revving. They are therefore favoured choice for racing engines for frequent engines speed and gear change conditions.
Dual mass flywheels
Dual mass flywheels are designed to have two flywheels connected as a single piece with one side attached to the crankshaft and the other side to the clutch assembly. A set of high-strength springs found between the two discs will act as a sponge to dampen the damaging of torsional spears and protect the gearbox, thus reducing the noise and engine vibrations. These flywheels will also improve fuel efficiency by allowing efficient use of engine power.
Flywheel manufacturers produce single and dual-mass flywheels suitable for a wide range of shaft sizes and structures. It is used across varied industries such as automotive, oil and gas, agricultural, off-highway, warehousing, and industrial for its intended purpose.
Flywheel materials
To attain excellent performance and durability, it is necessary to choose the right flywheel material, especially in the oil/ gas, railways and automobile industry.
Cast iron flywheels
Cast grey iron flywheels are cost-effective, have good castability and wear resistance nature, but it is ideal for vehicles engines that run less than 6000 rpm. Nodular iron or ductile iron is preferred over grey iron for its impact resistance, elongation and yield strength ductile properties.
Billet steel flywheels
These are stronger compared to iron and used for high rpm engines. These are the ideal option for race cars, trailers and trucks which requires high horsepower and high performance.
Billet aluminium flywheels
Using aluminium flywheels will reduce weight from the rotating assembly of a conventional flywheel by 10 to15 lbs. It has a lower moment of inertia to provoke an instant response to deliver faster acceleration and deceleration and suppress the wheel rotation. These are not expensive, and the installation process is not arduous.
Other factors
High Compressive Strength: it implies the pressure that metal can undergo without changing its form or shape. Ductile iron has higher compressive strength compared to other metals.
Durability: longer shelf life of the products is achieved by using high strength materials while casting flywheels. Easily breakable products are not preferred; that is why flywheel manufactures stick to produce more durable and unbreakable products with refined materials.
High Strength to Weight Ratio: Ductile iron or aluminium material has a high strength to weight ratio, making it easier for flywheel manufacturers to create lightweight castings in a cost-effective manner offering up to 50 per cent savings on weight over grey iron castings.
Resistant to Corrosion: Corrosion causes a great deal of wear and tear damage in high rpm machines. Hence, it is advisable to use high strength flywheels to avoid frequent repairs and maintenance.
Flywheels are known for their energy storage capacity. They have a wide range of applications in wind turbines, mechanical workshops, punching machines, automotive industries and even used in satellites to control the directions. Selecting the flywheel based each industry intended purpose will enhance the effective and efficient performance of machines.