Cast iron and wrought iron are substances with unique capabilities,…
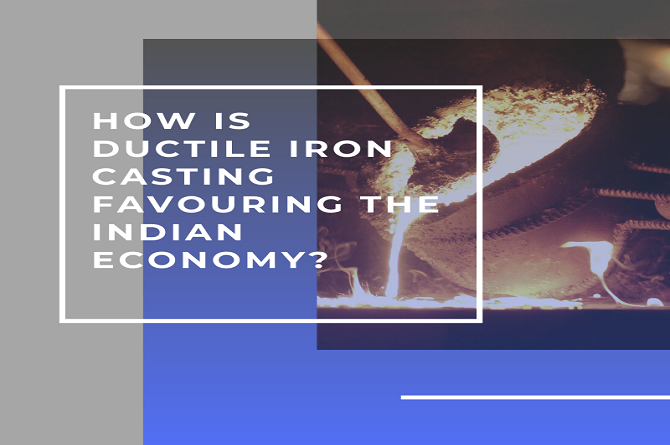
How Is Ductile Iron Casting Favouring The Indian Economy?
Foundries across the world are increasingly using high-quality ductile iron for casting a vast range of custom industrial applications. Compared to ordinary gray iron, ductile iron has significantly higher mechanical strength, flexibility and impact resistance properties – and as such, it is considered ideal for designing manhole covers, pipes, wheels & gear boxes, sturdy machine frames, automobile components & accessories, and other related products. To keep pace with the evolving industry needs and technological advancements, the top cast iron and ductile iron manhole cover exporters in India are regularly upgrading their portfolio to deliver optimal value for buyers. Over here, we will do a quick roundup on how ductile iron is facilitating the growth of the Indian foundry ecosystem:
By Delivering Superior Elasticity and Flexibility
Alternatively referred to as nodular iron or spheroidal iron, ductile iron has its custom microstructure, which lends greater ductility and overall mechanical strength to the material. The carbon content in ductile iron generally ranges between the 3% to 3.9% mark (which is significantly higher than the carbon content in cast steel). With greater strength and durability, ductile iron castings are finding usage in more and more applications.
By Ensuring Robust Impact-Resistance and Compressive Strength
Enhanced machinability and overall reliability are key hallmarks of good-quality ductile iron. The greater fluidity and tensile strength of the material eliminates chances of ductile iron manhole covers and other products getting accidentally damaged. The mechanical fatigue levels are minimal even after long periods of use. Thanks to the comparatively higher impact-resistance of ductile iron, cutting or drilling the material is a lot easier, while customised surface treatments can be done as well.
Easy To Weld; Has Better Shock Absorption Capabilities
Leading cast iron manhole cover exporters in India make use of ductile iron for structural weldings. In general too, the better weldability of ductile iron is an important factor behind its widespread adoption at foundries. The considerably higher damping capacity of ductile iron (compared to steel) ensures excellent shock absorption capabilities as well. While gray iron has an even higher damping capacity, it tends to become non-elastic at low stress levels.
The Machining Advantages Of Ductile Iron Are Excellent
The top ductile iron product manufacturers, like Crescent Foundry, use premium grade raw material (e.g., ductile iron with GGG 50 gradation) in their manhole covers and other casting products. The presence of relatively high volume of silicon in ductile iron enhances overall machining capabilities – while the better spindle speeds and considerably higher feed rates add to the overall usability and handling convenience of ductile iron. The material also has optimal depth to diameter drilling proportions.
Ductile Iron Is Lightweight & Has Top-Notch Dimensional Accuracy
The weight of ductile iron (on average) is nearly 8-10% less than most steel alloy varieties. The lightweight nature of ductile iron makes it easy for foundries and cast iron manhole cover exporters in India to arrange for product shipments in an efficient and cost-effective manner. The dimensional accuracy and strength-to-weight ratio of ductile iron are important factors as well, while the anti-corrosion assurance makes it an ideal material for water pipes and wastewater pipes.
Available In A Wide Range Of Sizes and Load Ratings
Better customisation and quality commitment make the top manhole cover manufacturers stand out. The load ratings of these products typically range from A15, B125 and C250, to F900. Depending on the precise nature of applications, the sizes of ductile iron products can vary (from the relatively compact 12”x12” types to the 48”x48” clear opening varieties). The leak-proof assurance, powerful locking provisions and painting options (epoxy, black bitumen, and others) contribute to the popularity and usability of ductile iron further.
By Ensuring Minimal Brittleness and Top-Class Abrasion Resistance
In comparison to most other types of iron, ductile iron is significantly less brittle in nature – while the elongation and elasticity properties are much higher. As a result, the different grades of ductile iron can be used in the ‘as-cast’ state – even before additional heat treatments are done. The leading manufacturers also make it a point to use ductile iron with smooth surface finish and complete abrasion resistance. This property, in particular, makes it ideal as the material for designing high-friction products & systems (e.g., engine crankshafts).
The Best Ductile Iron Manhole Cover Exporters In India Offer Complete Quality Assurance
Cutting-edge ductile iron sewerage and drainage applications in particular, and industrial tools & accessories in general, have emerged as important components of the growth in the Indian infrastructure sector. To ensure quality standard maintenance and optimisation, manufacturers typically adhere to the latest ASTM and EN-124 standards. Quick turnover times are ensured, and a large number of production-ready designs are made available. Prestigious certifications, like ISO 9001:2015 and ISO 14001:2015 underline the quality-commitment of the top manufacturers.
By Offering An Ideal Blend Of Yield Strength, Elongation and Tensile Strength
With a tensile strength that generally ranges from 60000 psi to a maximum of 1,20,000 psi, ductile iron is by far the better choice than gray iron for manhole covers, axles, gearboxes, crankshafts, pipes & fittings, valves, suspension system components, and other such products. The elongation of ductile iron is also high, while its yield strength is several times more than standard gray iron. In terms of surface hardenability as well, ductile iron delivers superior performance.
The Economical Choice
In order to deliver the best value to customers and drive the Indian casting ecosystem forward, manufacturers & suppliers follow agile & cost-effective production technologies. Since the cost of manufacturing is managed effectively, the ductile iron products are made available at competitive rates. In terms of performance, efficiency, reliability and durability, ductile iron is – more often than not – better than gray iron and many low-alloy steels.
The value of the worldwide iron casting sector is projected to go beyond $140 billion by the end of 2030, with the CAGR for the 2021-2030 period being well over 7%. In sync with the robust global trends, the Indian foundry market is also growing at an exponential rate. Thanks to its various advantages, use of ductile iron in industrial tools is steadily becoming mainstream. The industry has bounced back strongly from the pandemic-related slowdowns – and going forward, ductile iron in particular, and quality-optimised casting products in general, will continue to drive the Indian economy forward.