Brakes are essential for any automotive vehicle for its functionality…
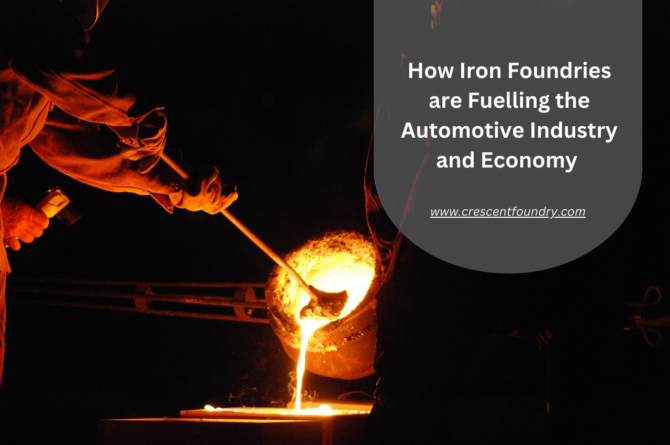
How Iron Foundries Are Fuelling the Automotive Industry and Economy
A CAGR of ~5% is indicative of the steady rate at which the worldwide market for automotive casting products & components is growing. The Indian market is keeping pace with the global trends, with demand for quality-assured casting products escalating rapidly. The role of leading automotive castings manufacturers is extremely important in this context. In addition to vehicle body parts, these companies are also coming up with precision-engineered transmission components, engine parts and related accessories.
Let us here take a look at how the top cast iron foundries are driving the automotive casting industry & economy:
By Serving As One-Stop Automotive Casting Product Suppliers
Cast iron applications for automobiles vary widely in terms of their nature and purpose. As the sector is getting more and more advanced, buyer requirements are also evolving. The top manufacturers and suppliers are adding value by including the complete range of auto components and accessories in their portfolio – right from high-performance brake rotors and flywheels, to brake callipers that improve the process control of automotive systems, drums, and more. In addition, steering systems and braking systems are also being designed, along with lock barrels and vehicular safety mechanisms. Through a seamless combination of design precision, engineering excellence and sheer variety, these foundries are taking the auto casting sector to an altogether higher level.
By Delivering On Their Promise of Quality and Trust
For the most reputed casting manufacturers, it is not only about selling automotive castings. These companies are making it a point to adhere to stringent quality parameters at every stage of manufacturing. Since in-depth quality checks (QC) and testing are being done, glitches (if any) are being identified and ironed out at an early stage. In fact, the unwavering commitment to quality of leading companies, like Crescent Foundry, has helped them expand their clientele across the globe.
With a focus on coming up with cutting-edge automobile castings that meet the precise needs of customers, the leading foundries are also utilising state-of-the-art infrastructure facilities. Streamlined processes are being followed, to ensure on-time delivery of personalised auto casting products. Since the cost of production is also being managed effectively, the foundries are being able to offer these products to buyers at competitive rates.
Note: The world-class production facilities at the disposal of the top foundries also help in optimising annual capacity of automotive casting manufacturing.
By Offering A Mix Of Enhanced Design Flexibility and Process Replication
The process of designing the frame inside which all the other auto components are housed has to be handled with careful attention to detail. That’s precisely what the best automotive castings manufacturers in India are delivering. The enhanced design flexibility is ensuring that auto castings of different shapes & sizes – and for varying use cases – can be designed with ease. Since easily ‘repeatable’ steps are followed during manufacturing, that makes the entire process quicker, error-free, and boosts average product turnaround times. For the best cast iron products manufacturers, the focus is always on keeping the primary structure of auto castings constant – and working around it, to improve the features, capabilities and product designs in an incremental manner.
Note: The ISO certifications of the top automobile casting component suppliers in India bear testimony to the value they bring to the table.
By Ensuring High Durability With Minimal Maintenance Requirements
The automobile industry, both globally as well as in India, is growing at a rapid clip. The challenge for automotive castings manufacturers is to adhere to the Just-in-Time (JIT) production requirements – while ensuring that the service lives of their products are not hampered in any way.
With an eye on this, the top foundries are regularly coming up with world-class automotive casting products (along with cast iron products for other industries) that rank high on the reliability and overall durability counts. The high mechanical strength of these products make sure that wear & tear – even after extended usage – are minimal, and frequent repairs / replacements are not required. What’s more, the maintenance requirements for sophisticated, precision-designed cast iron auto components are also pretty much straightforward (without much expenses or manual effort). The onus is on buyers to select a top foundry, and source products from it – which would deliver excellent value for money.
By Having A Steady ‘Customer-First’ Approach
The top foundries are using the latest, proprietary technology to design cutting-edge automotive castings. The workflows they follow are powered by expertise, a sound knowledge base on foundry business, and an unwavering ‘buyer-first’ approach. Right from product prototyping, machining and tooling, to pre-production and final manufacturing – everything is done while keeping the exact needs of the customers in mind. Relatively complex auto casting shapes are being designed, to meet evolving requirements.
Most, if not all, automotive casting tools and equipment, are heavy in nature. As such, users often face problems while handling them. The best foundry companies are focusing on coming up with relatively lightweight alternatives that offer the same level of durability and operational efficiency. Product handling ease is being enhanced, as a direct result.
By Ensuring Recyclability And And Protecting Environmental Integrity
Concerns over ecological balance are at an all-time high. Manufacturing companies, in particular, need to make sure that their day-to-day activities are not harming the environment in any way. Once again, leading auto casting manufacturers in India are taking up a strong stand in that regard. Strong environmental sensitivity considerations are being maintained – and the easy recyclability of the products enhance their value further.
With the growing popularity of electric vehicles (e-vehicles), automotive casting manufacturers are also coming up with housings that are precision-designed, have thin walls, and can provide the requisite level of protection to the built-in sensors. In general too, modern-day auto castings make sure that the telematics system of cars are shielded in an ideal manner.
By Understanding Challenges And Delivering The Right Solutions At The Right Time
A hallmark of all good cast iron product manufacturers for automobiles (and other sectors, for that matter) is their ability to grasp the precise challenges and pain-points of buyers. Many of these companies invest considerable time, effort & money for continuous research – to get actionable insights on probable product requirements. Doing so enables the foundries to come up with solutions that exceed customer expectations, deliver the best ROI, and ensure the best outcome in terms of functionality & efficiency.
By Working Towards An Unified Vision Of Building A Stronger Casting Ecosystem
Reputed automobile casting manufacturers are working in unison, to make the overall product ecosystem stronger. Right from expanding their product portfolios, to implementing innovative technologies to bolster productivity levels – the companies are pulling out all the stops to make sure that buyers always get casting products of the finest quality.
To cater to customer requirements in the best possible manner, the best automotive castings manufacturers in India typically follow systematic project management schedules to ensure quality and on-time delivery. Having world-class infrastructure facilities and implementation of the latest casting technology are also things that are common at these companies. Over the next few years, the automotive casting market will continue to evolve – both in India and overseas – and the top casting manufacturers & suppliers are certainly up for the challenge.