The market for industrial castings in India is growing fast,…
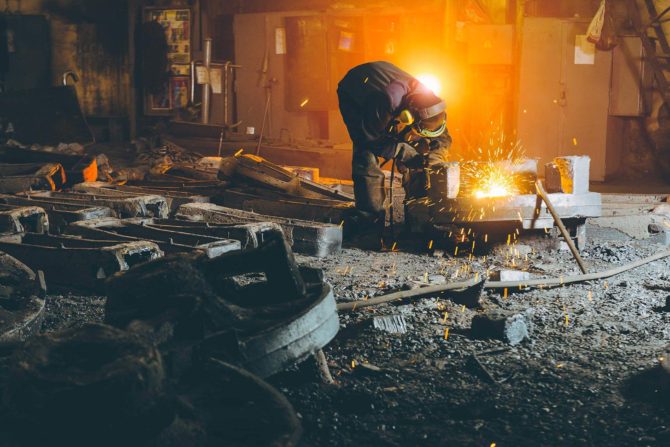
Best Industrial Equipment Manufacturers- Cast Iron Foundries
Foundries cast a significant role in enhancing every stereotype industry through their metal castings. Metal castings function in the modern world in many ways than most of us realize. These castings have been part of our everyday lives and continue to make our living more competent and effective. As we speak of its importance, foundries play a significant role in crafting these metal components exclusively for varied industrial purposes. Top Industrial equipment manufacturers deploy state-of-the-art techniques.
The foundry sector produces a massive amount of industrial equipment serving distinct applications in defense, aerospace, automobile, agriculture, oil and gas, railways, construction, mining, municipal, health care, and many others. The Indian foundry industry has grown incredibly in recent years with its valuable expertise, innovative technology, and capability to share a prominent place in the global market. Industrial equipment manufacturers produce goods with precise specifications and supreme quality to adhere to international buyer’s needs. To cope with the transforming world, manufacturers are creating products with technology interventions like 3D modeling, CAD/CAM, implementing quality checking at every stage of the process, and many others. Top foundries strive their way to perfection to attain utter customer satisfaction.
Industrial equipment is made by casting process by pouring liquid metal into moulds, where it cools and hardens into the specified shapes. Even though the principle is simple, there are many variations in metal casting methodology. To take intent from idea to reality, designers and engineers must be precise about the end products’ physical characteristics and aesthetic needs. A clear view of the design’s complexity and what sort of stresses the final product must withstand helps the manufacturers determine the metal type. A Good casting design is a matter of knowing all the elements and methods involved in getting an elite quality product as defined by customers. Foundries, as the metal components’ birthplace, assist varied industries through innovation and continuous developments as modern-day advances.
Intricate and Customs designs
Everything from buildings and architecture to our automobiles and kitchenware relies on foundry units. Many industries rely on manufacturing and casting foundries to create their unique machinery components. Many manufacturing companies face a challenge finding a solution to create the custom parts needed for their industrial projects. In this modern era, engineers and designers have the liberty of technology inventions to develop innovative and intricate designs. It enables foundry operators to create smooth, flowing designs, versatile and robust products.
Top foundries have the necessary tools and skilled professionals to create custom components. The 3D modeling enhances the modern foundry casting techniques to ease out the process. This particular technology makes it easier for foundries to collaborate with clients to craft unique components with complex shapes or complicated internal shapes. It enables the fabricators to show the clients what the product will look like before it comes off the assembly line. This metal casting style is incredibly flexible, allowing industrial equipment manufacturers to choose about any size, shape, type, and thickness of metal. This 3D modeling technology aids the engineers to identify and eliminate problems before production. The casting units ensure that the products are produced by adhering to every industry type’s specifications and needs.
Adoption of a variety of casting methods
Every industry type requires a unique set of metal castings. Metal castings have been the backbone of every industry, from agriculture to buildings to all household appliances. Therefore different types of casting methodology are followed for typical industrial applications. The specifications, size, and variety of materials required for industrial equipment will determine which type of casting method will suit the project’s best.
- The investment casting method is suitable for multifaceted and thin layered metal parts. It offers a high- level accuracy and top quality finish on final products.
- Sand casting is best suited for silica-based materials for more significant components and has minimal risk of flaws with costing less.
- Plaster casting uses gypsum and water as a strengthening compound to create moulds. This casting method is primarily used for creating large complex shapes with high-level accuracy ensuring smooth finishes.
- Permanent mould casting is a low-pressure process using reusable moulds, and it is best suitable for creating hollow shapes.
- Die casting is mainly used for zinc alloys. It is used for obtaining uniform design, compact shape, size tolerances and less post-casting machining.
Top-quality deliverables
Top iron casting foundries follow a set of quality checking procedures to identify the defects. This enables them to find problems beforehand and helps them to sort out the issues before getting worse. These procedures are an essential step for every industrial equipment manufacturer to ensure that the clients receive top-quality deliverables. Regardless of the automation level, the foundries always work towards improvements and experiment with designs that will enhance production. The precision and accuracy in designs will ensure high-quality with a high production rate. This characteristic further helps to decrease scrap loss and the cost of production. Again, the latest technology is put to use to eliminate product defects and inconsistencies. Thus enabling the metal components manufacturers to offer quality products at a reliable cost to their clients.
Alliance with the industries
Any top industrial equipment manufacturer or foundry casting unit works closely with its clients to identify their needs at an early stage before developing products for them. Together they understand the market trends and offer innovative solutions to ease out the operation process mutually. The Indian foundries have a vast knowledge about the varied industry type requirements, with their expertise and experience, craft equipment for various industrial applications such as agriculture, oil and gas, health care, automobile, railways, defence, construction, mining etc. From every moving vehicle to buildings and bridges, every industry depends on foundry castings. Foundries produce various industrial equipment from gearboxes to counterweights to aid the world function.
Metal castings are integrated with human life in one way or the other. Today, most household appliances and automobile industries cannot survive without foundry castings. This modern world has intervened in technology in every aspect. Foundries make use of these technological advancements to craft unique products as per each industrial need. In the foundry industry, an emphasis on technology enables manufacturers to increase production with premium quality products. High quality is attained through inspection and testing in every stage of the production process. The precision and accuracy of the products will lead to a win-win situation for both clients and industrial equipment manufacturers by minimizing production costs. Foundries are responsible for supporting society’s current standard of living and industrial development of the countries.