Every day, a vehicle’s brakes are applied multiple times. With…
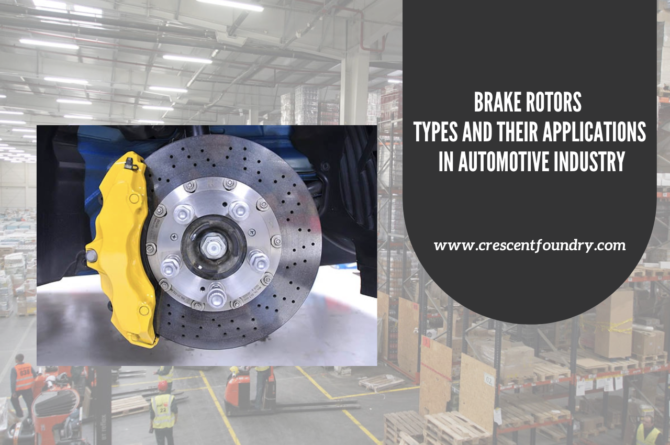
Brake Rotors – Types And Their Applications in the Automotive Industry
The automotive industry relies heavily on casting to produce parts such as engine blocks, transmission cases, and suspension components. These components need to be highly precise and accurate to minimise chances of error and misfit when assembled. This is the process of casting is preferred. Top automotive casting manufacturers in India offer casting products made with high precision and produced in large quantities at a relatively low cost. Although such products enjoy their presence in industrial, agricultural, and municipal markets, they are particularly important in the automotive industry.
Casting Products in The Automotive Industry
Casting allows for the production of parts with complex shapes that would be difficult or impossible to manufacture using other methods. This is especially important in the automotive industry, where parts must be able to withstand the stresses of high speeds, high loads, and harsh operating environments. Some of the major components produced by the casting process include the interiors of the vehicle, air conditioning & engine parts, braking system, and so on.
Here, let’s find out more about one of the major components of the brake system in an automotive machine.
Brake Rotors: Their Types
Brake rotors are circular discs that are connected to wheels in the braking system. There are several types of brake rotors, also known as brake discs, that are used in vehicles. Brake calliper manufacturers recommend choosing high-quality brake discs or rotors to endure maximum braking efficiency. Here are some common types of brake rotors.
-
Solid brake rotors:
These are the most common type of brake rotors and are made from cast iron. They are durable and inexpensive, but are prone to warping and may produce more brake dust than other types of rotors.
-
Slotted brake rotors:
These rotors have slots or channels cut into their surface to help dissipate heat and gases that build up during braking. They also help to remove debris from the brake pads, which can improve braking performance.
-
Drilled brake rotors:
These rotors have holes drilled into their surface to help dissipate heat and gases. They also help to remove debris from the brake pads, but they may be more prone to cracking than slotted rotors.
-
Cross-drilled brake rotors:
These rotors have both slots and holes drilled into their surface. Naturally, this provides even better heat dissipation and debris removal. They are often used on high-performance vehicles like sports cars.
-
Carbon ceramic rotors:
These rotors are made from a composite material that is stronger and has great heat resistance. They are lightweight and can improve braking performance, but they are also much more expensive than other types of rotors.
Brake Rotors: Their Applications
Brake rotors, also known as brake discs, are an important part of a vehicle’s braking system. These rotors are designed to convert motion into heat energy. These are some of the main applications of brake rotors.
-
Assists in slowing down or stopping vehicles
Brake rotors are attached to the wheels of an automotive machine. When the brakes are applied, the brake callipers push the brake pads to come against the rotors. This causes friction, which ultimately leads the wheels to stop moving. This way, brake rotors assist brakes in slowing down or stopping vehicles from being in motion.
-
Cools down the braking system
Thanks to the rotors, the heat from the motion (kinetic energy) gets dissipated, cooling down the braking system. For example, a driver who frequently drives in high-performance or off-road conditions may opt for slotted or cross-drilled rotors, while a driver who primarily drives on the highway may be fine with standard cast iron rotors.
Brake Rotors: Their Function
Brake rotors are found on most types of vehicles, including cars, trucks, buses, motorcycles, and bicycles. They are typically located at the center of the wheel, between the tire and the hub, and are attached to the wheel using bolts or studs.
In a typical brake system, the brake pads are mounted on the caliper, which is a component that surrounds the rotor. When the brake pedal is pressed, the caliper applies pressure to the brake pads, causing them to clamp down on the rotor and create the friction needed to slow down or stop the vehicle.
Brake Rotors: Maintenance
Brake rotors are subjected to a lot of wear and tear, as they are constantly subjected to high temperatures and friction. As a result, as per the best brake calliper manufacturers, ensuring proper maintenance is of utmost importance in order for safety and maximum efficiency. As a result, they need to be checked and replaced periodically.
Brake Rotors: Making the Choice
Brake rotors are generally chosen based on the type of vehicle, driving conditions, and the driver’s needs. For example, for a vehicle that frequently serves high-performance or off-road conditions, slotted or cross-drilled rotors are a better fit. On the other hand, for the highway standard cast iron rotors are appropriate. Besides, the material of the rotors also depends on the area of application.
TAKEAWAY
Top automotive casting manufacturers in India offer a range of brake rotors/discs for automotive applications. Since they play the part in a vehicle’s braking system (causing friction and ultimately bringing an automotive solution to a halt), it is important to make the right selection, backed up by proper maintenance.